ROTOR METER SAVES THE JERSEY ROYAL COMPANY £300,000 THROUGH TARGETED FERTILISER APPLICATION
In the last six years, one of the UK’s leading potato growers has saved over £300,000 through an unconventional but highly effective use of Stocks AG’s Rotor Meter.
As well as saving a significant amount of money by working with Stocks AG, The Jersey Royal Company has also helped Jersey’s government improve the quality of the island’s drinking water.
In 2016, having discovered that Jersey’s drinking water contained more than 50 mg / litre of nitrogen, the island’s Environment Minister published a five-year Water Management Plan. Delivering the plan relied heavily on working effectively with the newly formed Action for Cleaner Water group, which brought together Jersey Water, the Department for the Environment and the farming community.
As a key member of the Action for Cleaner Water group, The Jersey Royal Company was determined to do all it could to help the group achieve its aims. Mike Renouard, business unit director, who represents The Jersey Royal Company in the group, asked engineering manager, Ricky Gallon, to look at solving two key objectives, which would reduce the amount of nitrogen the company uses in its fields. First, Ricky was asked to find a way to reduce the amount of fertiliser the company was using. Secondly, he was tasked with finding a way of applying fertiliser in a much more targeted way.
Before 2016, like most potato growers, The Jersey Royal Company used a spreader to apply fertiliser to its fields before hand-planting. Ideally, the company wanted to place the fertiliser directly into the row underneath the tubers.
Disappointed with the accuracy of combining a wheel-driven applicator and power harrow and faced with limited machinery options on the island, Ricky returned to his roots to find a solution.
Originally from Wisbech in Lincolnshire, Ricky spent seven years working for RG Herbert, which had its factory just a stone’s throw away from Stocks AG.
“Having spent considerable time looking at what was available to us, I knew we needed something different to what was commonly used on the mainland. We needed something that would suit the unique nature of Jersey’s farmland,” says Ricky. “That’s why I picked up the phone to Stocks AG. I knew if anyone could help us, it would be them.”
The challenge was accepted, and just a few weeks after receiving the enquiry, Stocks AG’s R&D team had successfully customised a Rotor Meter to deliver what Ricky was looking for.
Stocks AG developed the Rotor Meter in the 1990s as a gravity-fed, metered one, two or three outlet applicator. For more than 30 years, the Rotor Meter has been popular with growers applying seed, granules, pellets and micro granule fertiliser.
For The Jersey Royal Company, which required higher output rates, Stocks AG developed a way to mount and control a fourth hopper.
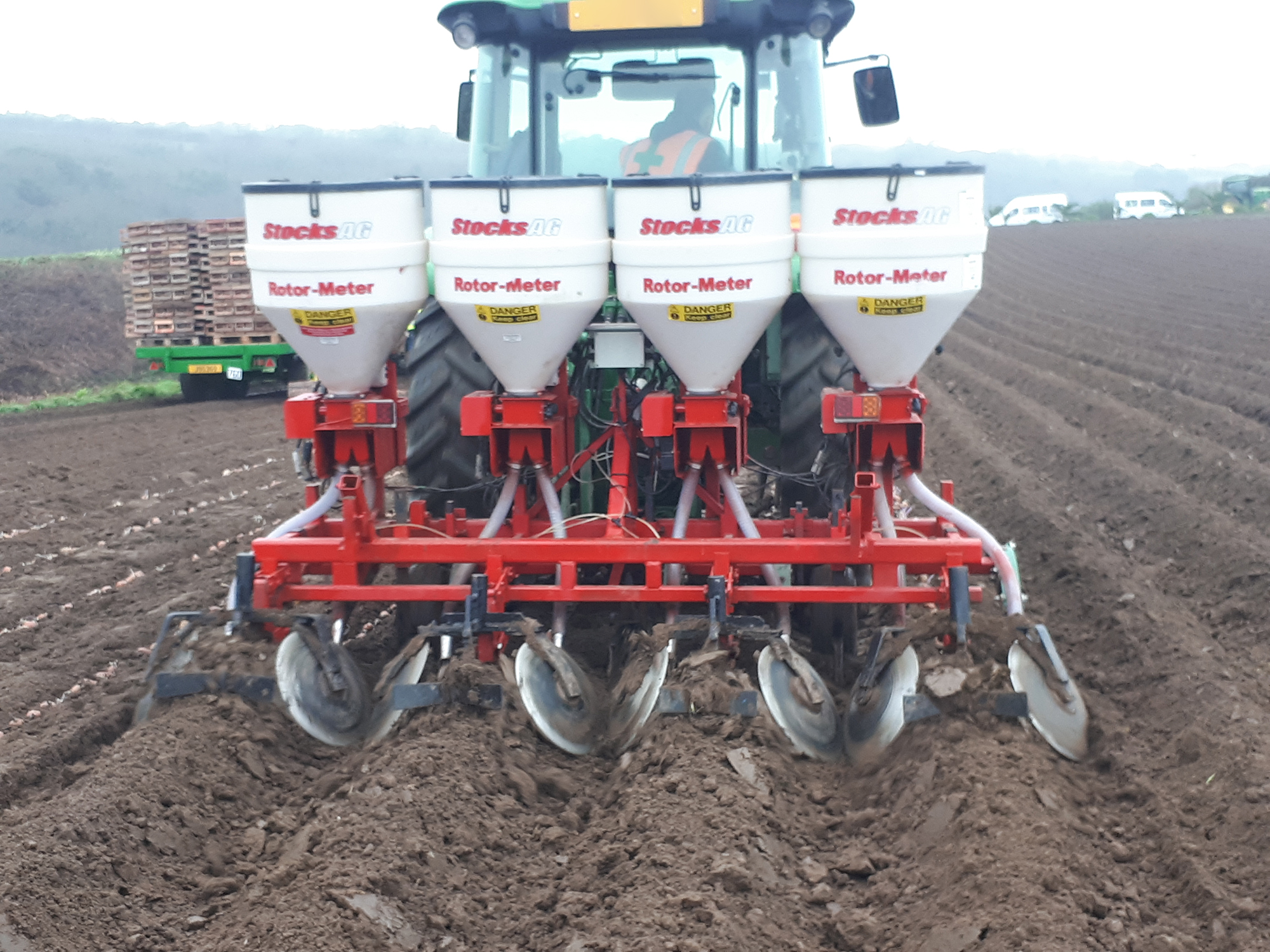
“The solution our team came up with offers everything Ricky was looking for,” says David Goodale in Stocks AG’s Technical Sales team. “We engineered a way to place four hoppers on a planter, with each hopper having one outlet.”
The Jersey Royal Company first used the innovative Rotor Meter set-up for 2016’s season, achieving a 15% reduction in fertiliser use. Ricky and the team were so impressed that they ordered four machines for the following year’s planting. An additional two units were added in 2020 and 2022.
In 2020 Stocks AG developed the i-CON system to control and maintain pre-set application rates and subsequently fitted it to The Jersey Royal Company’s machines. Further reductions in fertiliser use followed.
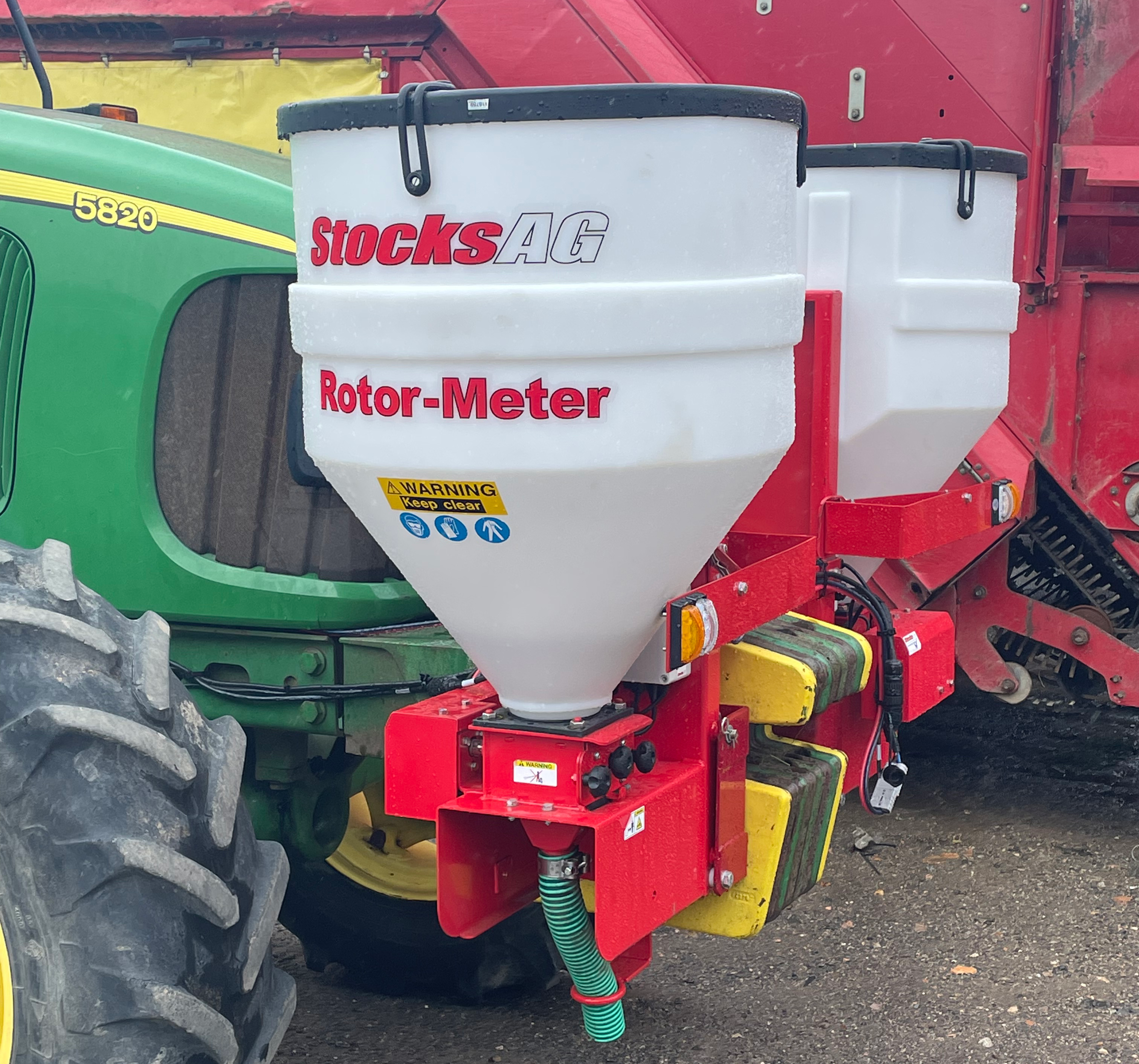
“As part of the government’s water management plan, each of our fields is graded red, amber or green for the presence of nitrates,” explains Ricky. “We farm 1,600 fields, with an average area of just two acres! Each field’s nitrogen grading is stored in the cloud, and the driver accesses this remotely via a tablet or phone. Then with just a few selections on the touchscreen, they’ve set the i-CON system to deliver the right application rate to suit their location. We save so much time by having a touchscreen and access to remote information. It’s a fantastic system for us and makes the Rotor Meter so easy to use.”
As well as ease of use, the 24 Rotor Meters that The Jersey Royal Company operates have enabled the team to reduce their fertiliser use to just 1,000 tonnes per season, a 15% reduction compared to 2016.
“We are really happy with how the Rotor Meters perform, and the cost savings they have created means they pay for themselves in just one season, says Ricky. “Over the six years of using the Rotor Meter in this way, I think we’ve saved over £300,000 in fertiliser costs. Perhaps even better than the financial benefits is that since introducing the Rotor Meters, the presence of nitrates in our fields is now under 40 mg per litre.
“I think the next step will be to see if we can use GPS data to plot fertiliser application in even more detail, which will reduce the amount we use even further, leading to better water quality and further financial savings!”
David Goodale is expecting other growers to follow The Jersey Royal Company’s lead as they seek to lower input costs.
“With fertiliser prices rising rapidly in 2022, reducing input costs has become a priority for all farmers, not just The Jersey Royal Company,” he says. “Running in parallel with cost savings is a desire to increase precision while at the same time looking after the land.
“The Jersey Royal Company wanted to see its fertiliser working at the point of sowing and not running off the surface during rainfall. We used our engineering experience to develop a solution that achieves both objectives. It’s great to know that the water quality in Jersey has improved and that The Jersey Royal Company has managed to save over £300,000 since using the Rotor Meter in this unusual but effective way.”
BUILT IN THE UK
Wisbech is still the home of Stocks Ag. All applicators are fabricated, assembled and painted in the Cambridgeshire factory. Precision assembly and quality control are paramount to the production process.
The R & D team work with both the factory and farmers to deliver a seeding solution that is fit for current farming practices.